How mines control driverless trucks

Technology correspondent
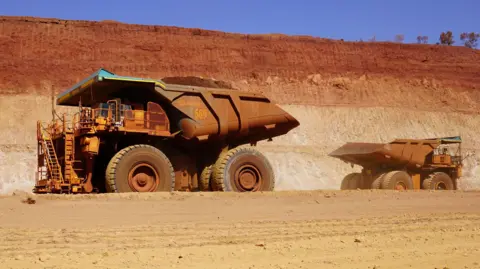
Do not get much more than that. I am in western Australia inner, at the Great Rio Tinto mine in Iron Namuli.
It is about two hours a trip north of Perth in an area called Bilbara.
Nobody lives permanently here. There are about 400 workers on the site at any time, and they are transported, and they work between four and eight days, depending on the transformation pattern, before flying home.
Giant trucks size of cities, capable of transporting 300 tons, crossed red roads in various sections of the open mine complex.
For a stranger like me, its size is scary enough, but hitting this feeling is to know that there is no driver on the wheel.
During a tour of the site in a natural company vehicle, one of the trucks is displayed, where it approaches a side road.
It sighed with relief because it turns brilliantly and continues in the direction that we just came. “Did you make you feel uncomfortable?” The driver of the car, Duan Paltin, the director of production.
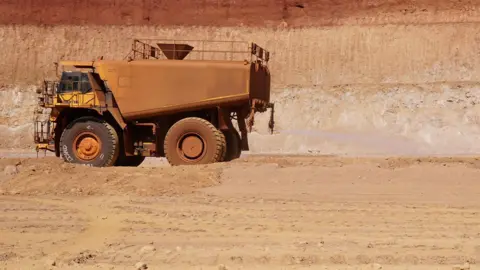
Greater Namutldi has a fleet of more than 50 self -driving trucks operating independently in pre -defined sessions, along with a handful hand handcrafted and operating separately in a different part of the mine.
Experiments are also a self -governing watercarton known as Henry, which, along with hand -paid roads, highlights mines to maintain dust down.
The company’s vehicle where I am able to work along with self -government trucks only because it is equipped with a high -resolution GPS, allowing it to be seen within a virtual system.
Before entering the independent mine area, we logged into this system and controlled a control unit via the radio that we were visible.
It surrounded our car in a virtual bubble “sees” self -driving trucks that cause them to manage its proximity by slowing down or stopping when necessary.
The touch screen in the cabin is displayed by all of the autonomous and independent vehicles and other equipment in the vicinity, along with the “ear lines” that show the immediate methods that self -driving trucks intend. If you looked at the screen instead of inconvenience, I would have seen that the truck would turn.
In addition to all vehicles that are provided with the large red emergency button that can stop the system, independent trucks contain lasers and front and rear radars to detect the risk of collision.
Sensing devices also discover obstacles. If a large rock falls from the back of the truck, the sensors on the next truck will notice this and the car stops.
However, some trucks look very sensitive – in my tour, I see a couple who were simply thwarted by off -road.
The coordination and monitoring of these robots is the Rio Tinto Operations Center (OC) in Barth, about 1500 km (930 miles) to the south.
It is the center of the nerves for all of the company’s Pilbara Iron Ore operations, which extends to 17 mines in total, including the three formed Namuculdi.
Steering from here by control units, includes more than 360 self -driving trucks in all locations (about 84 % of the total fleet); Mostly, a long -distance auto -distance rail network to transport the raw ore to the ports facilities; About 40 independent exercises. OC staff also remote control of factory and port functions.
Self -rule is not new to Rio’s Pilbara operations: I have started in the late first decade of the twentieth century.
It is also not unique: Australia has the largest number of independent trucks and mines that use automation of any country, and other mining companies in Pilbara use technology as well.
But the Rio scale has grown its operations here, including in Greater Namuculdi – which contains one of the largest independent truck fleets in the world – gives it global importance.
It is a global trend. According to Globaldata The number of self -driving trucks has decreased around the world almost over the past four years to more than 2000, mostly by Catpeberler or Komatsu.
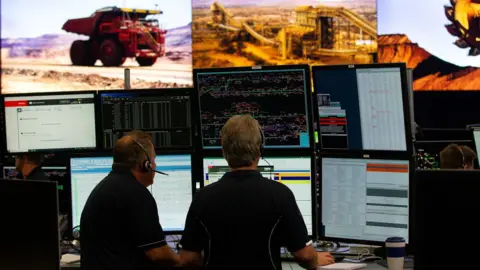
Matthew Holc, Managing Director of Belbra Company at Belbra Company, says the biggest reason for the introduction of this technology is to improve the material safety of the workforce.
Mining is a dangerous occupation: heavy machines can be operated unexpectedly by people who can also tire. “The data clearly shows that through automation, we have safer works,” says Mr. Holcz.
It also improves productivity – to about 15 %, as estimated. Independent equipment can be used more because there are no gaps due to changes or separators. Self -judgment trucks can run faster when there are less equipment than employees at the scene.
Such automation does not come cheap. Rio will not reveal what she spent on the total flight of Bilbara Automation so far, but the observers have put it in billions of dollars.
Meanwhile, job opportunities have evolved. The narration may be one of the robots that take care of jobs, but this does not seem to be here yet.
While OC has about one console per 25 independent trucks – according to Rio, no one has lost his job due to automation.
Instead, there was a redeployment: truck drivers joined OC as units that govern themselves, reinstalled to operate different parts of the equipment, such as excavators, luxuries and overwhelming, or went to drive handicrafts in different locations.
On the floor of the large open scheme in OC, amid the banks of the monitors arranged in groups for different mines, I met Jess Koy, who used to be a handbag but now, independently of the central drilling pitch. “I still put holes on the ground … only without dust, noise and stay away from the family,” she says.
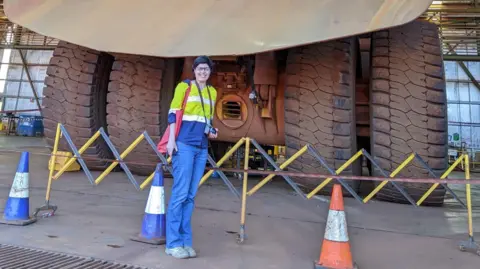
“Step Change” in terms of safety in the mining industry says, Robin Burgis Limrick, a professor at Queensland University in Brisbane, who studies human factors in mining. But this does not mean that there is no room for improvement.
Professor Burgis Limreik analyzed accidents that involved independent equipment reported to the organizers.
As he sees them, the facades used by employees in the field and in control centers to obtain information are not optimally designed. There were positions in which field employees lost awareness of the situation, which may be the best screen design. “Technology designers must do more to think about people,” he says.
There is also a risk that the burdens of control units can be overwhelming – it’s a crowded function and high risk.
Excessive confidence, as people become very confident that independent equipment will stop to the point that they begin to endanger themselves, and can also be a problem, and indicates that the effort should be directed to improve the ability of trucks to discover moisture. There were incidents caused by wet roads of losing traction.
Shin Rollston, coordinator of the Western Mines Alliance, who represents mining workers in Bilbara, says there are concerns related to legitimate safety with independent equipment.
He refers to a serious incident in May, when he criticized an independent train at the back of a broken train, which workers were repaired at the front end (they were evacuated before hitting but they did not ignore).
But Mr. Rollston praises Rio in general because of his time developing “some strategies, procedures and good policies” on how people interact with automatic vehicles.
Mr. Rollston expects that at some point, re -publication options will decrease and job losses. He says, “It is just mathematics from it.”
Meanwhile, the Rio Automation trip in Bilbara continues with more trucks and training and Henry’s water car. It is also seen closely working by Komatsu and Caterpillar for the development of unproductive, loaded and wines.
Late in the afternoon, waiting for Great Namuti Airport on the last flight to Perth, the announcement that it was canceled due to a problem with the plane. This 150 additional people will now need to feed and absorb them. It is not something for Rio, but I can only think that we are complicated people compared to robots.